CRAFTSMANSHIP

The Quality of Material
Challenging Ourselves to use Interesting
and Characterful Leather to Make Never-Before-Seen Shoes
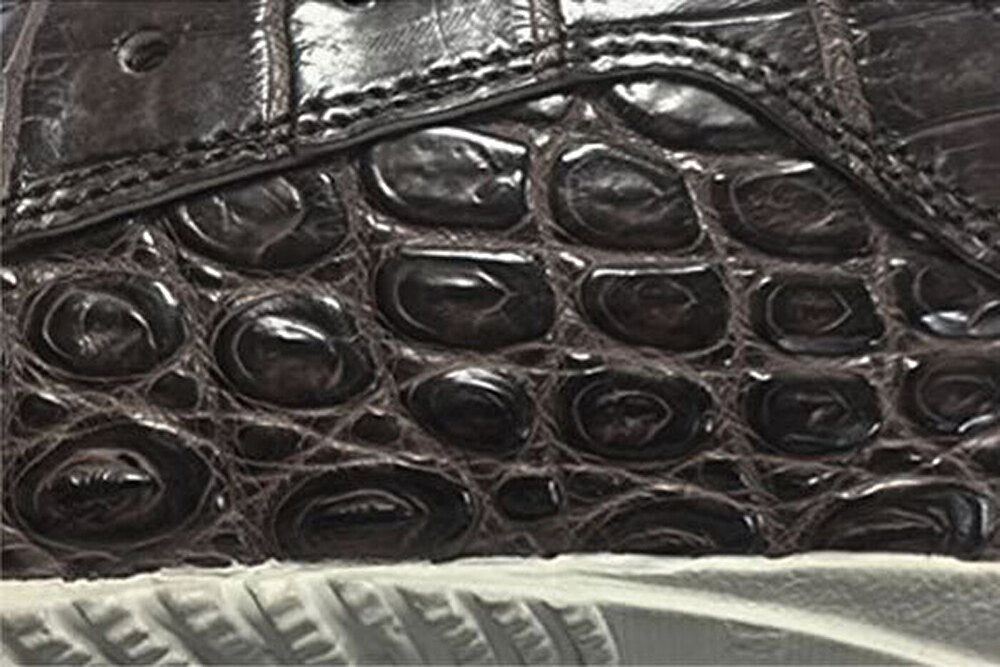
Materials not Usually used in Sneakers
At SPINGLE, we use leather which is not usually used in sneakers, and a variety of processes using a wide variety of leather to challenge ourselves to create shoes with a wide range of appearances and expressive character which is born through the various textures of each leather and during processing. The natural leather we handle includes kangaroo, cow, horse, pig, camel, goat, sheep, crocodile, python (snake), lizard, eel and as a rarity, shark. In processing, we handle print and pleat processing, crocodile processing, product dying which dyes the whole shoe, and washing processes which wash the produced shoes with water, and we also handle materials in collaboration with each brand.
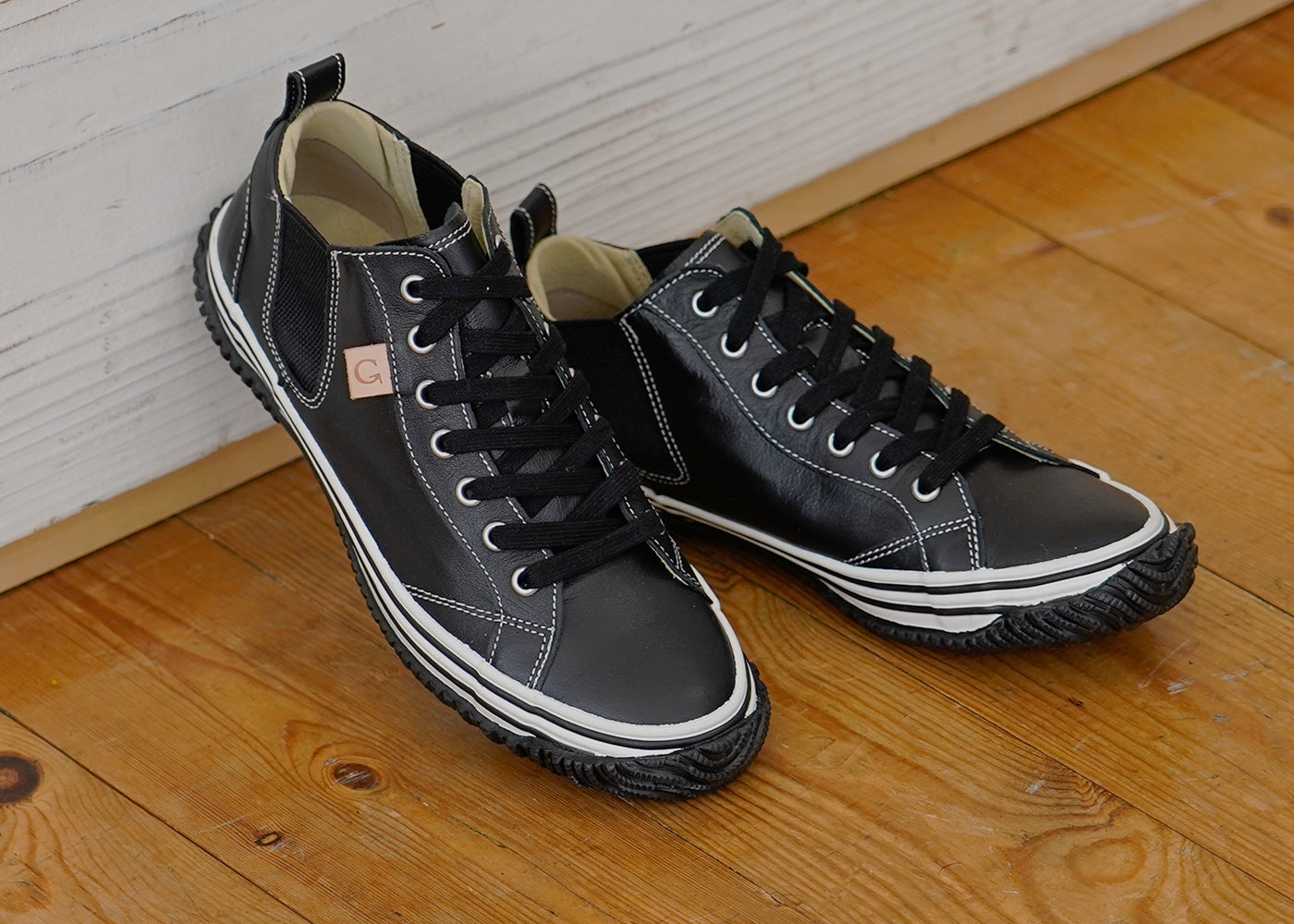
Shoes With Unique Character Made Possible by Hand Work
SPINGLE shoes are made in a high temperature kiln using the vulcanization process which involves high heat and carbonization, so we only use quality products which have passed strict checks on factors such as shrinkage and discoloration etc. Our commitment to these materials, which bring out the unique “character” of unevenness and wrinkles unlike any other pair as they are worn, and hand work, allows the creation of a one-in-the world pair of shoes with unique character. In the future we will continue to challenge ourselves to all possibilities in order to deliver to our customers shoes they have never seen before.

Vulcanized Sneaker
Great Time and Effort Used in Hand Work for
the Continuation of the Basic Sneaker Manufacturing Process, the Vulcanization Process

The Basic Manufacturing Process for Sneakers Began in the USA in 1839
The characteristic of SPINGLE is the unique design of the wave/makiage sole which envelops the upper. Of course, aesthetically this looks pleasing, but this form which is created using the “Vulcanization Process” also has the functionality of strong bonding of the sole and the upper, a sole which does not peel off easily and a shoe which does not lose shape easily.
The “Vulcanization Process” is a manufacturing process by which a rubber sole with sulfur added is glued to the shoe body and put in a kiln where heat and pressure are applied. It was invented by the American inventor Charles Goodyear more than 170 years ago in 1839 and is the true “basic sneaker manufacturing process.”
Craftsmen manually glue the upper (shoe body) to the sole and set the sneakers in the hanging shelves. Here, at first glance, the sneakers look close to their finished form, but actually the rubber part is still soft. By putting these in the vulcanizer, the upper and the sole are firmly bonded.

Hand Work Taking a Great Amount of Time and Labor
The sneakers are pressurized and heated in the kiln for about one hour at over 100 degrees Celsius. When the heating is finished, the kiln door opens upward with a roaring sound and smoke billows out. Amid the hot air, white smoke and rubber smell, craftsmen remove the hanging shelves and deftly cut the temporary threads and cloth which were used to prevent loss of shape. Next, a large fan is used to cool and stabilize the shape of the hot sneakers.
Due to the “vulcanization process” being basically hand work, a great amount of time and labor is taken, and production efficiency is poor. The number of companies in Japan using the vulcanization process has decreased sharply, and it is said that now, including our company, only very few remain. Our factory, which has over 80 years of history, will continue to protect the “vulcanization process” and continue to share this good quality with the world.
Craftsmen’s Voice
We Bring you the Voice of our Craftsmen who are Essential for our Shoemaking

Design (Pattern)
Creating Attractive and Comfortable Shoes
We take care in balancing the fitting feel, such as a comfortable foot feel, and the design. To create a shoe which is attractive and feels comfortable when you wear it, great care must be taken because even a slight difference may rub the foot and cause pain etc.
Message
I really hope customers will love their shoes and enjoy wearing them.
I would be very happy if these are the shoes you just can’t help choosing when you go out.

Toe Lasting (Pulling Over)
Toe Lasting (Pulling Over)Ensuring Width is the Same With no Difference by the Millimeter
The task of lasting (pulling over) the upper over the wooden last and ensuring there are no wrinkles. The difficult part is that when there are decorative materials it is hard to make the left and the right symmetrical. Furthermore, if the materials differ, depending on the part the leather may stretch slightly differently, so it is necessary to align the left and the right sides by hand to balance them. If the left and right widths are different or the height does not match the shoes will look strange, so it is necessary to take the effort of using the analog style of matching to the same width by the millimeter to ensure there are no errors.
Message
I really want you to get into wearing these shoes to their full extent and feel their awesomeness. To those who want to treasure them, I hope you will take good care of them and clean them when they get dirty.

Lasting
Ensuring the Best Appearance and Ease of Foot Entry
Here the task of lasting the sides is undertaken, with the front completed by a machine, and the inside and outside sides attached to fit the last (foot shape model). Of course, this affects the appearance of the shoes so it is necessary to take care, because depending on the amount of pulling, the height of the collar may change, which can make foot entry difficult.
Message
I love recreational driving, and these shoes are easy to drive in, so I hope that you too will enjoy these shoes for both driving and walking when you go sightseeing etc.

Sole Attachment
Difficulty in Adjusting Each Sole to Match Each Shoe’s Condition
Here the finishing work of attaching the shoe sole is undertaken. In order to prevent the upper from peeling away due to gaps, we consider the type of upper material and select glue to match. Even with the same material, the degree of leather shrinkage differs from shoe to shoe, therefore fine adjustment is required, and even now curving the wave/makiage sole up to the toe tip is still difficult. I feel quite nervous when gluing difficult materials. There is a wide range of color variations, so I hope you will enjoy choosing and wearing them in various situations.
Message
There is a wide range of color variations, so I hope you will enjoy choosing and wearing them in various situations.